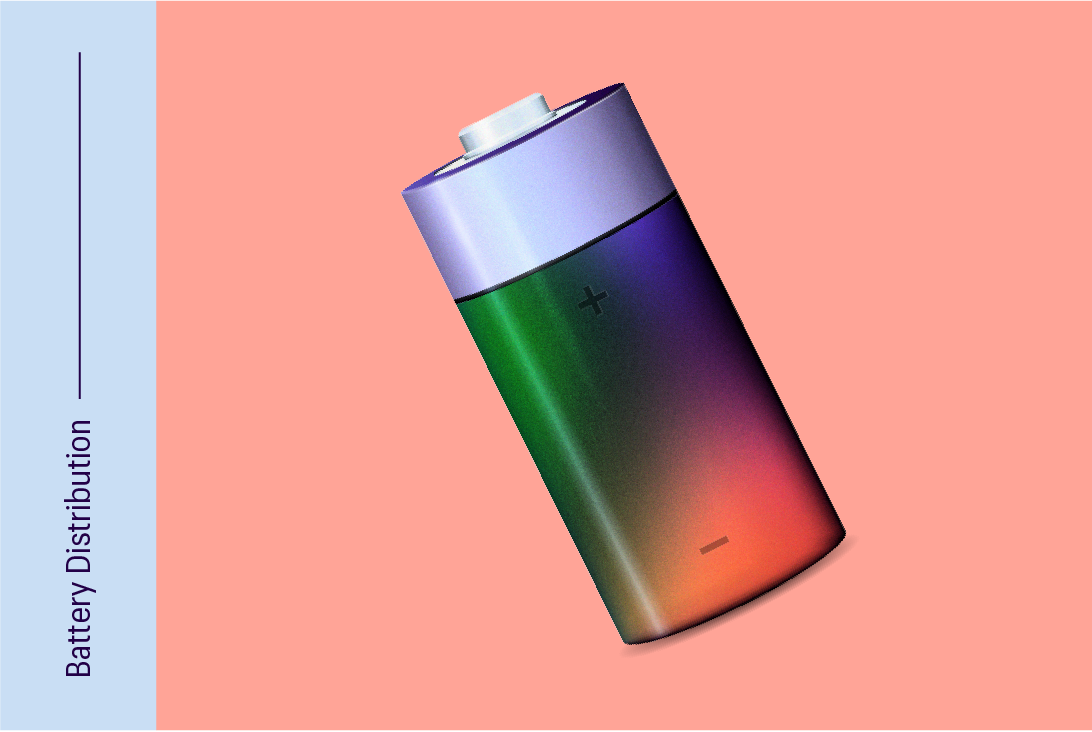
Problem Statement
Our client faced significant operational inefficiencies, including high costs from underutilized truck capacity and elevated labor expenses, as many trucks were not used to their full potential. Around 20% of their demand was met through non-scheduled deliveries, adding unpredictability and further costs. On average, trucks were loaded to only 78% capacity, with a utilization rate of just 32%, leading to considerable resource wastage. Additionally, load times averaged around 45 minutes per truck, worsening the inefficiencies. They needed robust demand forecasting to optimize truckload to improve operational efficiency, reduce costs, and enhance service delivery to meet customer needs more effectively.
Impact
- Reduced truckload factor by approximately 25% and decreased out-of-stock trucks per trip from 9 to 7.
- Estimated savings of 2 million with a one-time reduction in inventory carrying costs when the solution is scaled to the entire US.
- Expected savings of around 6 million over six years by switching to smaller trucks when the solution is scaled to the entire US.
- Other potential benefits: fuel savings, efficient loading, reduced non-scheduled delivery trips.
Access the Case Study to Learn More about This Partnership
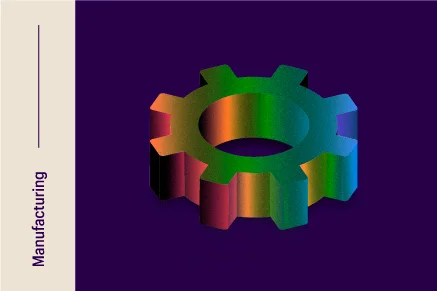
Monitoring Manufacturing Machinery
Frequent maintenance of machinery in manufacturing facilities can lead to downtime and increased expenses. By implementing real-time analysis and reporting dashboards, manufacturers can access vital data to proactively detect defects and deviations.
Read more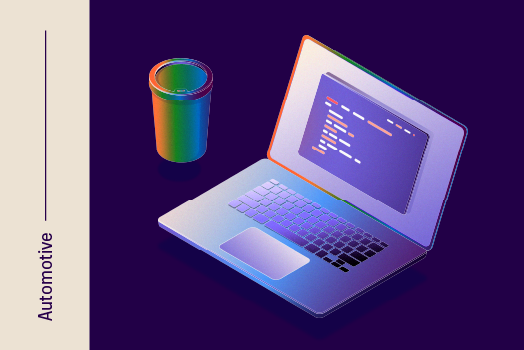
Developing MLOps Framework to Optimize ML Models
We developed a complete MLOps framework for a leading automotive OEM to optimize their ML models and business processes.
Read more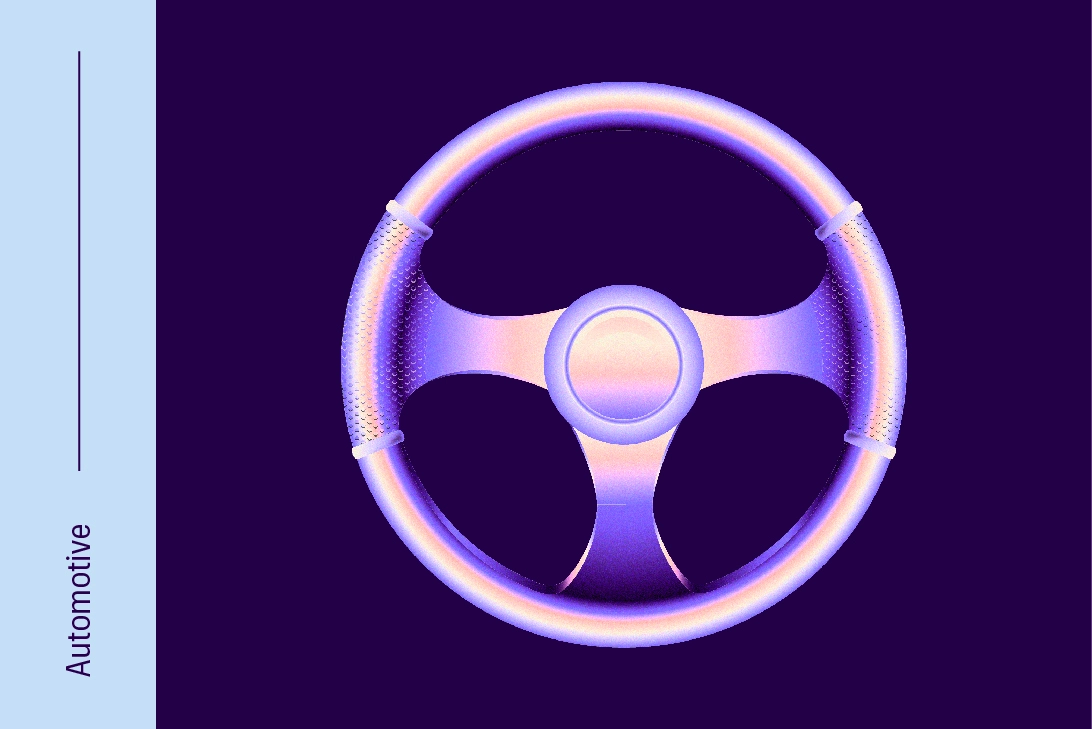
Optimizing Website Personalization through Next Best Action
We helped an automotive OEM increase their vehicle sales by implementing a custom website navigation experience that drives users toward their purchase path.
Read more