In the previous article of this series, we covered factors that paved the way for digital twin technology in CPG product manufacturing. We have elaborated about how digital twin models of manufacturing processes aid to draw discrete information that drives future courses of performance enhancements and quality control in the CPG product manufacturing framework. In the second part of this series, we’ll discuss the best practices that can ensure you make the most out of Digital Twin technology adoption.
Technology adoption typically entails skyrocketing Costs. So why get a Digital Twin?
Digital Twin is a concept and not a single product or a standalone piece of technology. A plethora of technologies such as the 3D simulation, IoT, 4G/5G, big data, blockchain, edge computing, augmented reality, cloud computing, and artificial intelligence translate this concept into a reality. With this dependency, it is also prudent to say that the expenses that accompany building digital twins are directly proportional to the cost dynamics of the supporting technologies. This apprehension over technology costs was strong up until recently when there has been an extensive adoption of digital twin technology across industries. This has further motivated technology service providers to minimize the costs of software platforms to give an impetus to the adoption of digital twins.
IoT– IoT platform serves as a technically advanced and economically viable platform that enables and enhances the performance of a digital twin model. An IoT digital twin offers a hybrid visualization of both real-time and historical data. This allows stakeholders to view all possible physical parameters associated with a product from a single source. Information that is not relevant is generally hidden to avoid visual clutter. From an economic standpoint, a major flux of IoT platforms in the business landscape has resulted in the advent of IoT sensor developers who have contributed to supply market competition, leading to a drop in the price of IoT.
Cloud computing– The cost of large data center networks is declining with improved access via cloud computing solutions such as software-as-a-service (SaaS). This is driving the feasibility of using and maintaining digital twins which are essentially compute and storage-intensive ventures. The liberty to pay only for the required computing power makes it an economically viable option over on-premise solutions.
Augmented Reality– Augmented reality has allowed digital twin models to break free from 2D confinement to a 3D rendering of digital insights. It enables the seamless merger of the digital model to its physical twin to facilitate an instant and real-time visualization of factors that can threaten the performance of the actual product. However, investing in such technology can be a costly proposition. This necessitates prudent associations with vendors who are known to deliver at rates based on the degree of expertise needed to develop AR. This will result in significant cost optimization for end-users.
Artificial Intelligence– Advanced machine learning algorithms are instrumental in designing models based on real-time sensor readings and historical data attributes rather than just the design information. These datasets derived from multiple assets aid in performance assessment and warn against any quality discrepancies.
Laying the foundation for optimal Digital Twin Technology utilization in the CPG industry:
Build a compatible ecosystem– An ideal technological ecosystem to drive the functioning of digital twin models should be populated with modelers who are conversant with a range of physics-based and analytical ML methods. The ecosystem should comprise of data scientists, ML engineers, domain experts, and business thinkers who can develop and execute digital twin capabilities and drive outcomes. However, their technical acumen loses value sans a responsive infrastructure that can ingest and curate a wide range of heterogeneous data sets that are quite typical to the CPG industry. These data sets are characterized by information ranging from a customer’s last purchase of an aerated drink to the texture of chocolate preferred by a customer. This brings both complexity and heterogeneity to datasets. A supportive infrastructure is extremely crucial to process such data sets and furnish tangible data models. Intuition is a much-needed aspect in this infrastructure to allow digital twin models to adjust to the ever-changing nature of data inputs.
Ensure that you are using the data right– The data at hand is going to determine the quality of results, laying emphasis on the capabilities in honing data. For the CPG industry, in particular, it finds even more relevance given the complexity and heterogeneity of data. These data characteristics substantiate a balanced approach towards finding the right amount of information to nourish digital twin models. Any aberration of the optimum data quantity can impact the level of its granularity. Another important step is to integrate and interrelate data gathered from sensors and inputted to the digital twin. It is recommended to upgrade the computing architecture of APIs as interfaces to process sensor data in bulk. This effectively reduces the processing time and burden on cloud architecture. One way of achieving this is to implement edge computing.
Need for digitization– CPG companies that embrace digitization will be better positioned to compete as the market shifts to more connected customers and customized products. Executives should be equipped with digital tools to share information, improve agility, productivity, and quality. It helps companies to pivot quickly and confidently, so they can address issues or take advantage of market opportunities with a digitally connected production network.
The availability of vast data lakes certainly tips the scale in the favor of CPG businesses. Despite being in its initial stages, stakeholders are fast realizing the beneficial prospects of implementing digital twin technology in CPG product manufacturing.
Roadmap to build and implement Digital Twin Models for CPG product manufacturing:
Recounting one of our recent experiences of collaborating with Fortune 500 enterprises, we successfully built and deployed a digital twin for a candy manufacturing unit of a leading CPG enterprise. The steps involved are highlighted below:
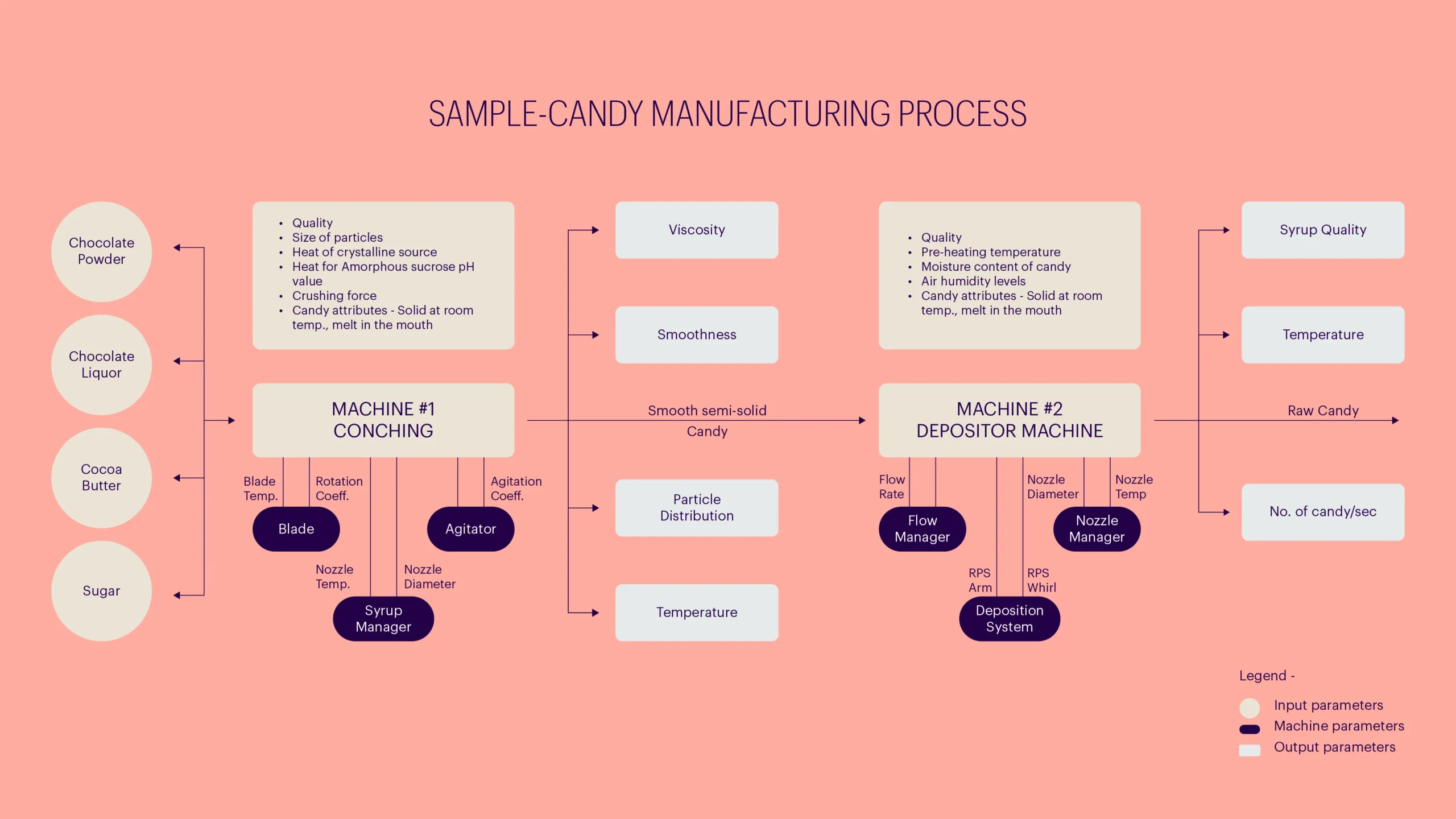
Exploration – Initial discussion with stakeholders to gather the necessary inputs to begin data pipeline development and consolidation. While doing so, we undertook frequent factory visits, conducted surveys with manufacturing plant managers. These activities allowed us a better comprehension of blueprints of the manufacturing process along with machine specifications, and supply chain mapping.
Build – A digital prototype of the twin model was built and its functional accuracy was monitored. Multiple simulations of the twin model were built and executed to reach optimum accuracy. The performance analysis of these simulated models issued necessary directions and an optimum accuracy level to create the digital twin model.
Execute– We commissioned the digital twin model of the manufacturing framework that generated data insights for monitoring and run diagnostics of the framework. Anomalies were detected that helped to devise contingency measures and adopting early warning systems accordingly to maximize efficiency gains.
Scale– The digital twin concept was contextualized to other production lines while monitoring its functionality with the other processes/systems. Lastly, we identified other use-cases for system optimization.
The four-steps solution framework above is an example of how digital twins can utilize multiple sets of data gathered from different sources to allow stakeholders to bring visible improvement in predictive maintenance while improving product quality and save time.
Potential use cases about CPG product manufacturing:
- Test product variations and changes, identify causes for process variability, detect defects, etc. digitally without shutting down the manufacturing line.
- Test out planned changes to the plant and augment production capacity, using the plant’s digital twin without stalling the regular manufacturing process.
- Is a cost-effective and efficient alternative to physical prototypes of manufacturing processes. Digital twin models require lesser to no manual intervention which can prompt operational difficulty and increase chances of human error.
- Reduce chances of false alerts that lead to mobilization of efforts to non-existent emergency conditions. This ramifies to significant production downtime and capital wastage.
- Allow flexibility to the dynamic demands of consumers. For instance, confectionery enterprises face extreme dynamism in consumer demand for variety in flavors, ingredients, texture, packaging, and labeling.
Reconfiguring business processes in any industry requires the right amount of investment, time, technologies, and ultimately the willingness to take the risk of disrupting the existing process. Given the constant consumer market dynamisms, adopting digital twin technology in the CPG industry is no more a choice but a dire necessity. With customer expectation being a chief driving force behind product development, digital twin model enables real-time visualization of disruptive market trends and building products that mirror consumer expectations, first perfected in its digital counterpart.