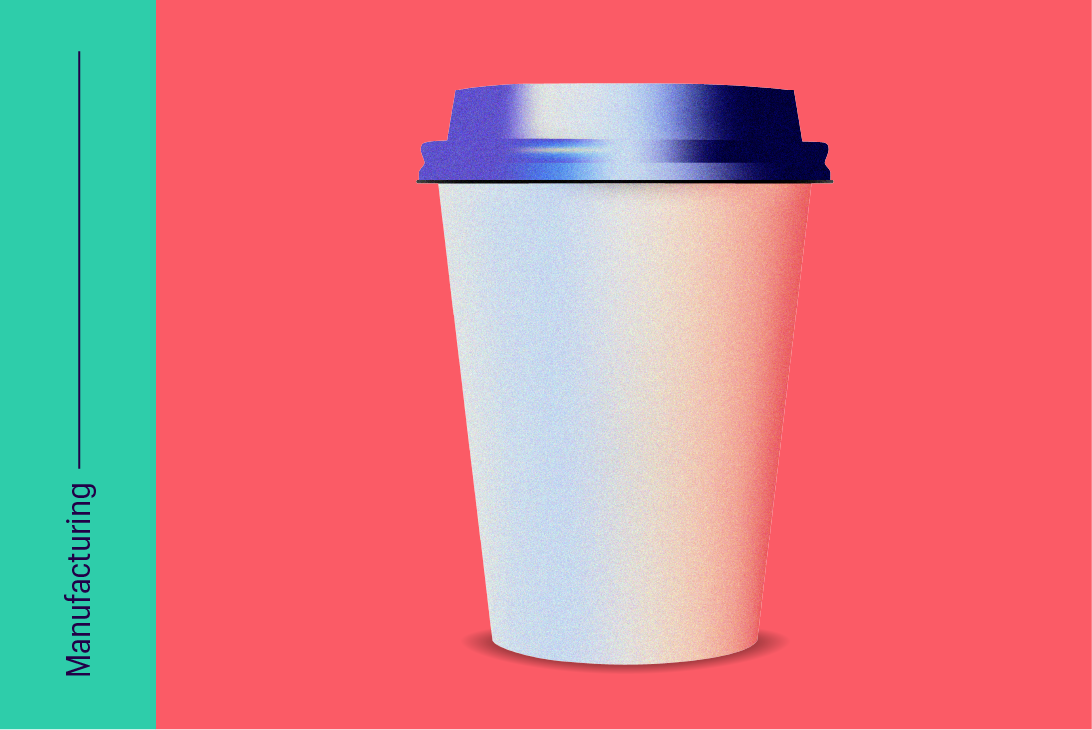
Problem statement
Our client, a top beverage maker, faced losses from expired products and missed deadlines due to siloed systems, manual processes, and poor data visibility. Delayed reporting, unplanned downtime, and limited collaboration hampered responsiveness. They needed an integrated solution to unify planning, scheduling, and execution, enabling real-time insights, scenario simulations, and data-driven decisions to boost efficiency and reduce disruptions.
Impact
- Achieved significant time savings by reducing report generation from over 6 hours to under 15 minutes per site per day
- Saved 6+ work hours per site per day, significantly boosting planner productivity
- Over 24,000 hours saved annually across all planning teams
- Scalable solution implemented across 6 manufacturing sites and 18 production planners.
Access the Case Study to Learn More about This Partnership
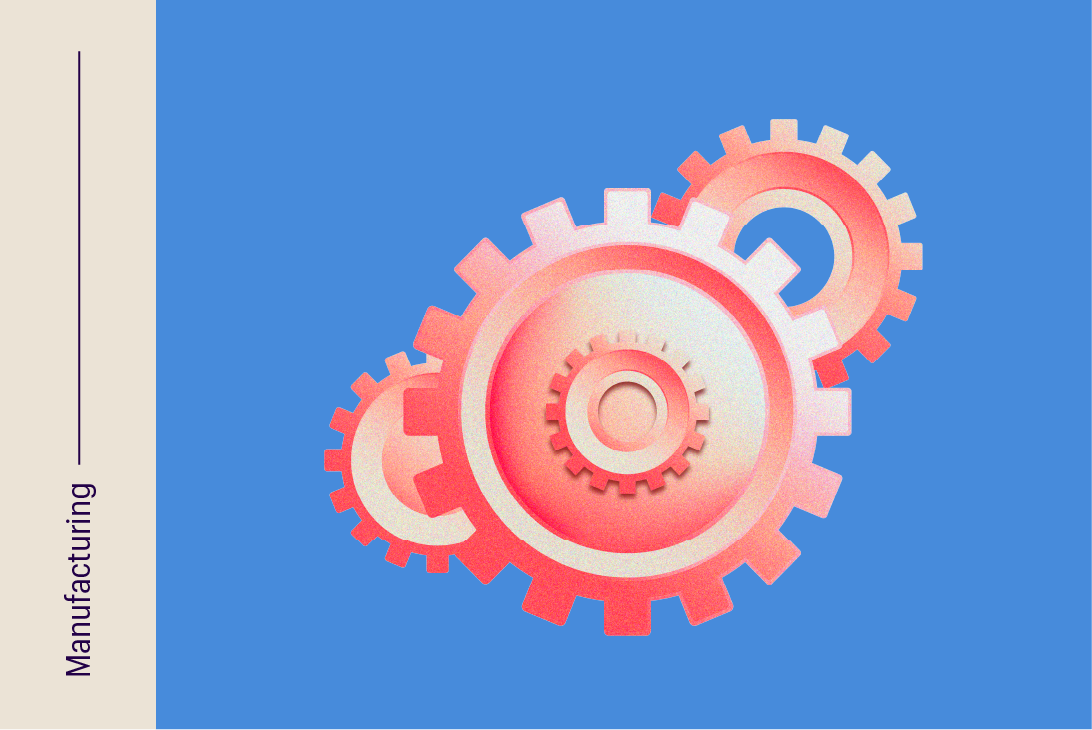
Minimizing Unplanned Downtime with Predictive Maintenance in the Manufacturing Process
Discover how we helped a pharmaceutical manufacturer reduce critical equipment failures by 40% and save $1M annually. Through a scalable, cloud-based anomaly detection framework, we optimized maintenance, improved efficiency, and ensured compliance.
Read more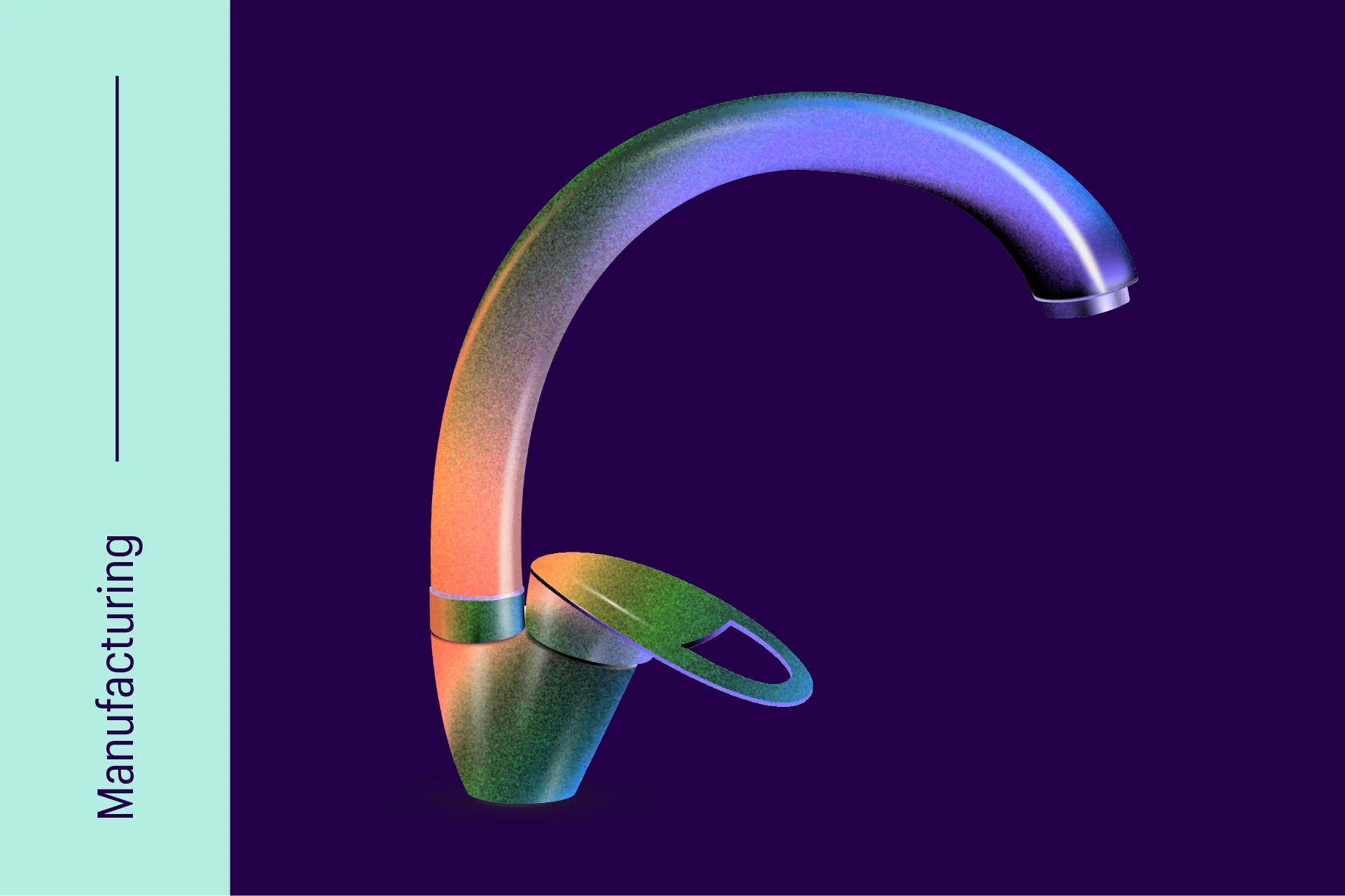
Manufacturing Demand Forecasting
We helped a leading plumbing giant discover an estimated $2 million savings in production costs using a manufacturing demand forecasting solution.
Read more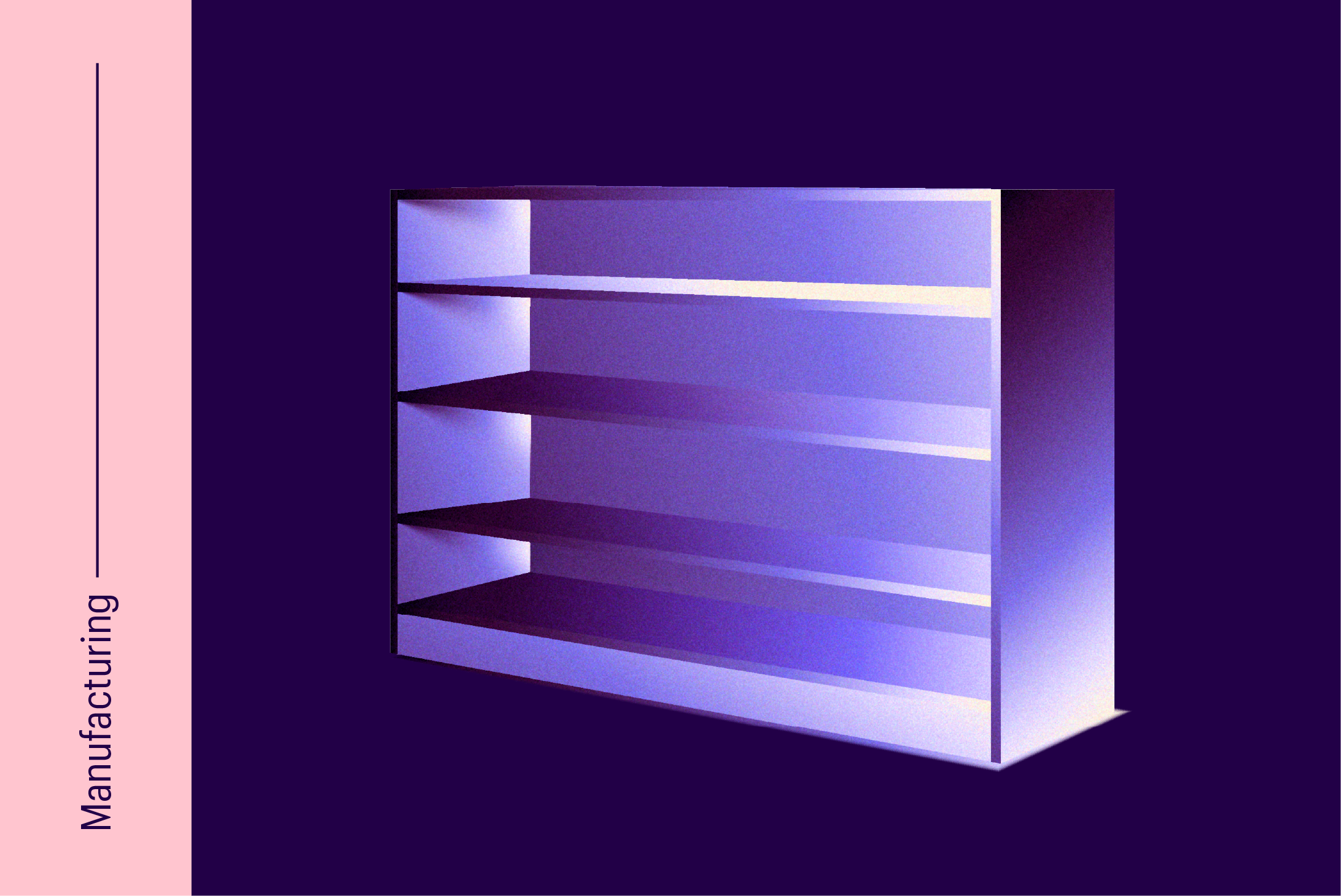
Enabling Data Trust and Efficiency in Manufacturing Through Master Data Management
Discover how we helped a leading manufacturing company overcome inefficiencies caused by fragmented data, duplicate records, and weak governance. Through our comprehensive MDM framework, we optimized data integrity, security, and integration, enabling streamlined operations, improved customer profiling, and better decision-making for long-term efficiency and growth.
Read more